Smart Manufacturing: Industry 4.0 and Connected Factories
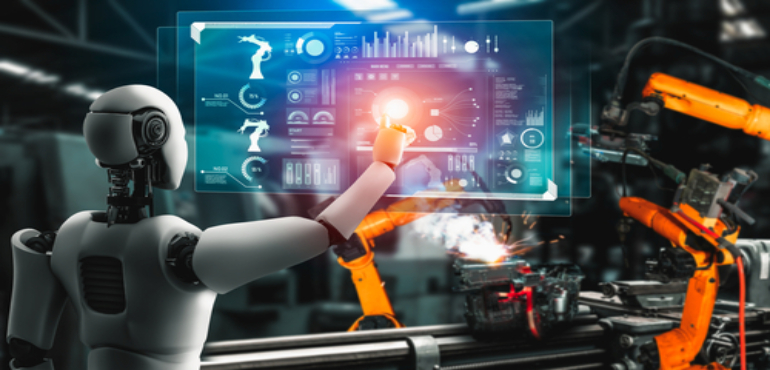
Welcome to the future of manufacturing - where Industry 4.0 integrates with connected factories in a symphony of intelligence and efficiency that is transforming production floors worldwide. Smart Manufacturing, as it's known, isn't just an idea or concept for tomorrow; it's creating revolutions today! Combining cutting-edge technology like IoT, AI, machine learning and big data analytics, smart manufacturing opens up entirely new avenues for cost optimization, productivity augmentation and unprecedented operational transparency. The era of dark assembly lines manually operated by labourers is fast receding into history. In its place emerges a new paradigm - vibrant factories humming with intelligent machines seamlessly communicating through digital networks - ushering us into Industry 4.0 epoch. This blog post delves deep into this fascinating world of interconnectivity within modern-day manufacturing units to present comprehensive insights about its potentials and challenges alike.
The Evolution of Smart Manufacturing
The evolution of smart manufacturing has been driven by the advancements in technology and the need for increased efficiency and productivity. Industry 4.0, also known as the Fourth Industrial Revolution, has brought about a transformation in the manufacturing sector, with the integration of digital technologies and automation. Smart manufacturing involves the use of sensors, data analytics, cloud computing, and artificial intelligence to optimize processes and make informed decisions. Connected factories enable real-time monitoring and control of the production line, leading to improved quality, reduced downtime, and cost savings. This evolution has also led to the emergence of new business models, such as servitization, where manufacturers shift from selling products to providing value-added services. Overall, smart manufacturing holds great potential to revolutionize the way products are manufactured, ultimately leading to more efficient and sustainable production processes.
Understanding Industry 4.0
Industry 4.0, also known as the Fourth Industrial Revolution, represents the ongoing transformation of the manufacturing industry through the use of advanced technologies and digitalization. It is characterized by the integration of cyber-physical systems, the Internet of Things (IoT), cloud computing, and artificial intelligence into industrial processes. This paradigm shift aims to increase production efficiency, flexibility, and quality by creating smart, interconnected factories. Industry 4.0 enables real-time data collection and analysis, allowing manufacturers to make data-driven decisions and optimize their operations. It also facilitates the automation and optimization of production processes, reducing human error and improving productivity. Furthermore, Industry 4.0 promotes the development of intelligent products that can communicate with each other and interact with their environment. Embracing Industry 4.0 concepts is essential for manufacturers to remain competitive in today's global market.
Key Components of Connected Factories
Connected factories, also known as smart factories, leverage cutting-edge technologies to create a fully integrated and automated manufacturing environment. The key components of connected factories include the Internet of Things (IoT), cloud computing, data analytics, and artificial intelligence (AI). IoT enables the interconnection of physical devices and sensors, allowing real-time monitoring and control of the manufacturing processes. Cloud computing provides the storage and computational power necessary for massive data processing, allowing manufacturers to access and analyze large amounts of data generated by the connected devices. Data analytics helps to transform this raw data into actionable insights, enabling manufacturers to optimize their production processes, improve quality, and reduce costs. AI plays a crucial role in connected factories by automating decision-making processes and enabling machines to learn from data and make intelligent predictions. Together, these components enable connected factories to achieve unprecedented levels of efficiency, flexibility, and productivity.
Benefits and Challenges in Implementing Industry 4.0
Implementing Industry 4.0, or the concept of Smart Manufacturing, offers numerous benefits for companies in various industries. One major advantage is increased efficiency and productivity. By implementing advanced technologies such as IoT, AI, and robotics, companies can automate processes, streamline operations, and increase output. This can ultimately reduce costs and improve overall profitability. Additionally, connected factories allow for real-time data collection and analysis, enabling companies to make data-driven decisions and identify areas for improvement. However, implementing Industry 4.0 also presents several challenges. One challenge is the integration of legacy systems with new technologies. Many companies already have existing equipment and processes that may not be compatible with the latest advancements. Another challenge is the potential disruption to the workforce due to automation. Companies need to ensure that employees are properly trained and can adapt to new roles in the digitized factory environment. Overall, while there are challenges, the benefits of implementing Industry 4.0 are promising for companies looking to gain a competitive edge in the global market.
Future Trends in Smart Manufacturing
As technology continues to advance, the future of smart manufacturing holds immense potential for further innovation and improvement. One key trend that is expected to gain momentum is the integration of artificial intelligence (AI) and machine learning into the manufacturing process. This will enable machines to analyze vast amounts of data in real-time, leading to predictive maintenance and optimization of production operations. Another significant trend is the adoption of the Internet of Things (IoT) in smart manufacturing, with sensors and connected devices enabling seamless communication between different components of the production line. This will result in enhanced efficiency, flexibility, and the ability to monitor and control operations remotely. Furthermore, the use of robotics is set to increase, with autonomous robots taking over repetitive tasks, while collaborative robots work alongside humans to improve productivity and safety on the factory floor. Overall, the future of smart manufacturing promises increased automation, agility, and responsiveness in meeting customer demands.